VFW SERIES
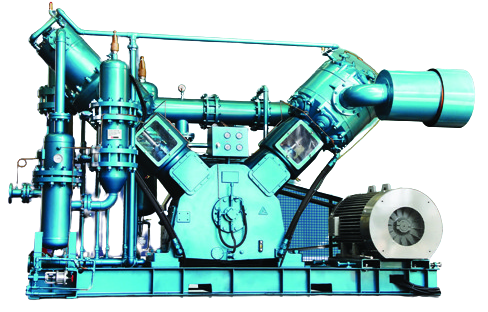
The air compressor for PET bottle blowing machine.
PET/PP bottle forming process
- Oven is steadily heated to provide the forming temperature evenly distributed over the bottle preforms.
- The mold is locked onto the transmission mechanism for bottle forming.
- Blow nozzle is inserted into the preform.
- Air is injected into the preform to form the bottle.
- The mold is opened.
- The finished product is unloaded.
- Mold stripping
Applications of blow molding
- The demand for (PET) bottle blowing is growing.
- VFW series compressors are designed exclusively for PET bottle blowing machines.
- he air compression process is 100% completely oil-free, allowing for the supply of oil-free, clean air.
- PET bottles and containers are recycled massively as the idea of environmental protection grows.
- The pressure of compressor is regulated between 25 and 40 kglcm?G, making the series suitable for various industrial oil-free applications.
- The primary applications are. for example. pharmaceuticals. food and packaging. paper making. textile. petrochemicals. bacteria culturing. chemical analysis and electronics/high-tech manufacturing.
Completely Oil-Free, Clean Pressurized Air
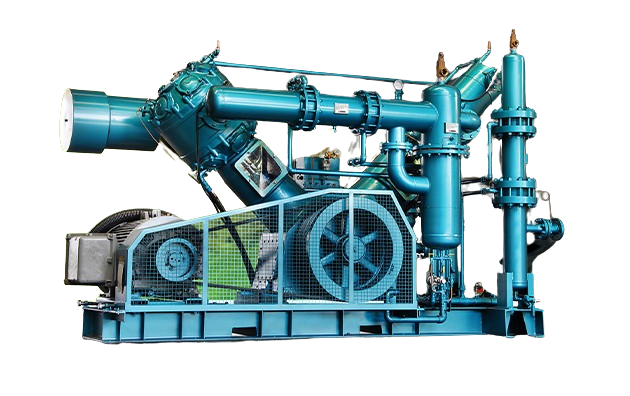
Design criteria for the body
- Driven by the crankshaft of oil pump, no additional power needed-
- Stainless steel suction / discharge valves for high strength and long service life.
- Pistons made of aluminum alloy for effective weight reduction and dynamic balance.
- Special coating on cross-head for better wearing resistance and smoother operations in the long run.
- Single-action design for the 2nd and 3rd stages, thus reducing the number of valves needed.
- Mono-block 2nd and 3rd stage pistons. no need for a-stage air-tight design,
- Compressor body encapsulated in a water jacket for effective cooling and increased life of parts and components.
- Piston rings made of PTFE, special formula that increases wear resistance and service life-
- Unique air intake baffling design for lower noises, smaller impulses and longer service life,
Complete details of equipment design
- High- level air filtering accuracy, suitable for various industrial environments.
- Al-in-one design for easy shipping by cargo container.
- Integral cooling water circulation design for easy pipe work installation.
- Designed for 20 to 30 years of trouble-free use when operated in normal conditions.
- Low-rpm design, i.e. longer service life for parts and servicing cycles.
- Special high-performance cooling design for more compact size, greater performance and higher efficiency,
- Latest defogging design and optimized condensation separation for greater compression efficiency.
- Wide range of work pressure allows regulation of pressure between 25 and 40 kg/cm G depending on operating conditions.
Our Standard Control
- Voltmeter
- Ammeter
- Power supply indication
- Water loss protection
- Oil loss protection
- operation timer
- Electric overloading protection
- Emergency stop button
- 3rd high temperature protection
- Auto / semi-automatic control switching
-
ON / OFF switch and indication
Additional functions are available as options on demand)
Maintenance and servicing
- Complete after service system across the globe.
- Optimization of service solutions by predicting service needs via indicators and trends.
- Use of high-strength composite materials for greater reliability of parts and increased life of components.
- Reciprocal compressor features ease of maintenance and all com n are easy to remove for servicing.
- Large bore and low rpm design features light loading an prolonged service life of valves, piston rings and bearings.
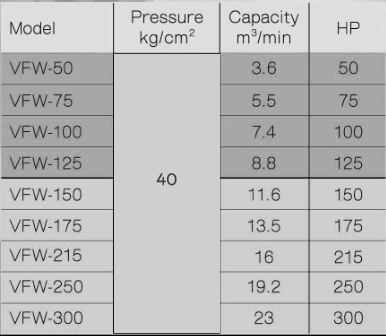